ASME B31.3 TP316L stainless steel Pipe Wall Thickness Calculation Response | ASTM A312
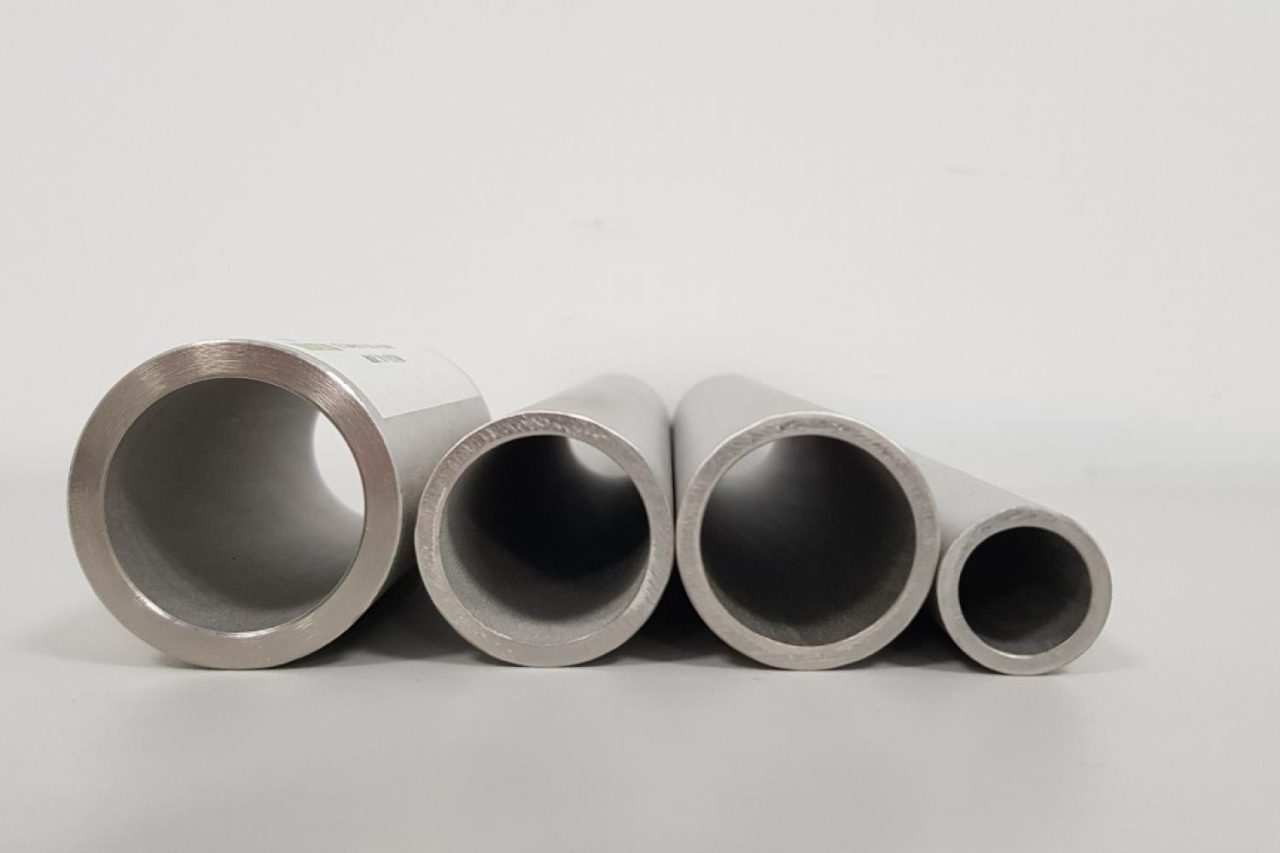
ASME B31.3 Pipe Wall Thickness Calculation Response
Let’s address your questions systematically, focusing on ASME B31.3 for your high-pressure water piping system using seamless TP316L stainless steel pipe (ASTM A312). I’ll provide clear answers to your questions about design pressure, bursting pressure calculations, and when to use bursting pressure charts, while clarifying the differences between design and bursting pressure.
1. What design pressure should I use? 250 bar, 290 bar, or higher?
Answer: For ASME B31.3, the design pressure should be the maximum pressure the system is expected to experience under normal or upset conditions, including any pressure relief or safety valve settings, with consideration for conservative design practices.
- Your system details:
- The pump’s pressure relief valve (PRV) operates at 250 bar.
- The safety valve is set at 290 bar.
- You’ve calculated using 300 bar as the design pressure.
- Guidance:
- Per ASME B31.3, the design pressure must account for the highest pressure the system could experience, including transient conditions or safety valve settings. The safety valve setting of 290 bar represents the maximum pressure the system is designed to handle before the safety valve activates.
- It’s common practice to add a margin to the safety valve setting to ensure the pipe can withstand pressures slightly above the relief point, especially for dynamic systems like high-pressure water with plunger pumps, where pressure spikes can occur.
- Your choice of 300 bar as the design pressure is reasonable and conservative, as it provides a small margin (approximately 3.4%) above the safety valve setting of 290 bar. This accounts for potential pressure surges or tolerances in the safety valve operation.
- Recommendation:
- Use 300 bar (4350 psi) as the design pressure, as you’ve done, to ensure the piping can handle the maximum system pressure with a safety margin. If you want to be less conservative, you could use 290 bar (4205 psi), but the 300 bar choice is safer for dynamic systems with potential pressure transients.
2. Verification of Your Calculation for Pipe Wall Thickness
You’ve calculated that a 1-inch Schedule 80S seamless TP316L pipe (OD = 1.315 inches) works for a design pressure of 300 bar. Let’s verify this using ASME B31.3 formula 3a from paragraph 304.1.2 for straight pipe under internal pressure.
Formula 3a (ASME B31.3, 304.1.2)
Where:
- t = Required wall thickness (in)
- P = Design pressure (psi)
- D = Outside diameter of pipe (in)
- S = Allowable stress (psi) = 16,700 psi for TP316L at 20–30°C
- E = Quality factor (1.0 for seamless pipe per ASME B31.3, Table A-1A)
- W = Weld joint strength reduction factor (1.0 for seamless pipe or at low temperatures like 20–30°C)
- Y = Coefficient for temperature (0.4 for austenitic stainless steel like TP316L at 20–30°C, per Table 304.1.1)
Given
- Design pressure, P = 300 bar = 300 × 14.5038 = 4351.14 psi
- Pipe OD, D = 1.315 in (1-inch nominal pipe)
- Allowable stress, S = 16,700 psi
- E = 1.0 (seamless pipe)
- W = 1.0 (seamless pipe, low temperature)
- Y = 0.4 (austenitic stainless steel at 20–30°C)
Step 1: Calculate required thickness
Step 2: Add corrosion allowance and mill tolerance
- Corrosion allowance: For high-pressure water in TP316L stainless steel at 20–30°C, corrosion is minimal. If no specific corrosion allowance is required, assume 0 inches. Confirm with your system requirements (e.g., water quality, potential for erosion).
- Mill tolerance: For seamless ASTM A312 pipe, the manufacturing tolerance is typically -12.5% of the nominal wall thickness. The required thickness must be adjusted to ensure the minimum thickness after tolerance meets or exceeds 0.155 in.
Step 3: Compare with Schedule 80S
- For 1-inch Schedule 80S (ASTM A312 TP316L):
- Nominal wall thickness = 0.179 in (per ASME B36.19M for stainless steel pipe).
- Minimum thickness after 12.5% mill tolerance = 0.179 × 0.875 = 0.157 in.
- The minimum thickness (0.157 in) exceeds the required thickness (0.155 in), so 1-inch Schedule 80S is adequate for 300 bar (4351 psi) design pressure.
Conclusion: Your selection of 1-inch Schedule 80S (OD = 1.315 in, nominal wall thickness = 0.179 in) is correct for a design pressure of 300 bar, assuming no significant corrosion allowance is needed.
3. How are bursting pressures in ASTM A312 stainless steel pipe charts calculated?
Answer: Bursting pressure for pipes, including ASTM A312 stainless steel pipes, is typically calculated using the Barlow’s formula or a similar theoretical formula for thin-walled pressure vessels. These charts provide the theoretical pressure at which the pipe would fail (burst) based on the material’s ultimate tensile strength (UTS) and the pipe’s dimensions.
Barlow’s Formula for Bursting Pressure
Where:
- P_b = Bursting pressure (psi)
- S_u = Ultimate tensile strength of the material (psi)
- t = Nominal wall thickness (in)
- D = Outside diameter (in)
For ASTM A312 TP316L
- Ultimate tensile strength (S_u) is approximately 70,000 psi (per ASTM A312, minimum UTS for TP316L is 70 ksi).
- For your 1-inch Schedule 80S pipe:
- t = 0.179 in
- D = 1.315 in
Calculation
Notes on Bursting Pressure Charts
- Charts are derived from such calculations, often adjusted for:
- Minimum wall thickness (accounting for mill tolerance, e.g., 87.5% of nominal thickness).
- Material properties (using minimum UTS from ASTM A312).
- Safety factors or simplifications (some charts may use conservative assumptions).
- Charts may also incorporate empirical data or modified formulas to account for real-world factors like material defects, seam effects (for welded pipes), or high-temperature reductions.
- For seamless TP316L pipes, the bursting pressure is based on seamless pipe properties, and charts typically list values for standard schedules (e.g., 40S, 80S).
When to Use Bursting Pressure Charts
- Bursting pressure charts are used to estimate the ultimate failure pressure of a pipe, typically for:
- Safety assessments: To ensure the system’s operating pressure is far below the bursting pressure (e.g., applying a safety factor).
- Design validation: To confirm that the pipe’s bursting pressure provides a sufficient margin above the design pressure.
- Non-ASME applications: In industries not governed by ASME B31.3, where bursting pressure is a primary design criterion (e.g., some hydraulic systems).
- For ASME B31.3: Bursting pressure is not directly used for pipe wall thickness calculations. Instead, the allowable stress (S) governs, which is typically set at a fraction of the UTS (e.g., 1/3 to 1/4 of UTS for stainless steel) to ensure a large safety margin.
4. Difference Between Design Pressure and Bursting Pressure?
Design Pressure:
- The maximum pressure the system is designed to operate under, including normal operation, transients, and safety valve settings.
- Used in ASME B31.3 calculations to determine the required pipe wall thickness based on allowable stress (S), which incorporates a safety factor (e.g., 16,700 psi for TP316L, much lower than UTS).
- Ensures the pipe operates safely within elastic limits, far below failure.
- For your system: 300 bar (4351 psi), conservatively chosen above the safety valve setting of 290 bar.
Bursting Pressure:
- The theoretical pressure at which the pipe would fail (burst) due to internal pressure exceeding the material’s ultimate tensile strength.
- Calculated using the material’s UTS (e.g., 70,000 psi for TP316L) and pipe dimensions, without safety factors.
- For your 1-inch Schedule 80S pipe: Approximately 1314 bar (19,057 psi), far above the design pressure.
- Represents the ultimate failure point, not a safe operating condition.
Key Differences
Aspect | Design Pressure | Bursting Pressure |
---|---|---|
Purpose | Safe operating pressure for design | Theoretical failure pressure |
Basis | Allowable stress (S), with safety factors | Ultimate tensile strength (S_u), no safety factors |
Value (for your pipe) | 300 bar (4351 psi) | ~1314 bar (19,057 psi) |
Use in ASME B31.3 | Primary for wall thickness calculation | Not used directly; for reference only |
Safety Margin | Large (e.g., ~4.4x bursting pressure) | None; represents failure |
Why the Difference Matters:
- ASME B31.3 ensures the pipe operates with a large safety margin (design pressure << bursting pressure) to prevent failure under all conditions, including fatigue, corrosion, or pressure spikes.
- Bursting pressure is a reference to understand the pipe’s ultimate capacity but is not used for design because it lacks safety factors.
5. Additional Considerations for Your System
- Pressure Transients: Plunger pumps can cause pressure surges (water hammer) due to rapid valve operation or nozzle clogging. Ensure the 300 bar design pressure accounts for these transients. If surges could exceed 290 bar significantly, consider a higher design pressure or surge suppression devices.
- Corrosion/Erosion: High-pressure water with atomizing nozzles may cause erosion at bends or nozzles. TP316L is corrosion-resistant, but confirm water quality (e.g., no chlorides) and consider a small corrosion allowance (e.g., 0.01–0.02 in) if erosion is a concern.
- Pipe Schedule Availability: Verify that 1-inch Schedule 80S is readily available and compatible with fittings and nozzles. If higher schedules (e.g., Schedule 160 or XXS) are needed for smaller diameters or higher pressures, recalculate.
- Fittings and Joints: ASME B31.3 requires that fittings (e.g., elbows, tees) and joints (e.g., welds, flanges) also meet the design pressure. Ensure all components are rated for 300 bar.
- Testing: ASME B31.3 requires hydrostatic testing at 1.5x design pressure (1.5 × 300 bar = 450 bar or 6527 psi). Confirm that the pipe and system can withstand this test pressure.
6. Summary
- Design Pressure: Use 300 bar (4350 psi) as the design pressure, as it conservatively covers the safety valve setting of 290 bar and potential pressure spikes. Your calculation for 1-inch Schedule 80S TP316L pipe is correct, with a nominal wall thickness of 0.179 in, which meets the required thickness of 0.177 in (including mill tolerance).
- Bursting Pressure Calculation: Bursting pressures in ASTM A312 charts are calculated using Barlow’s formula (P_b = (2 S_u t) / D) based on the ultimate tensile strength (~70,000 psi for TP316L). For your pipe, the bursting pressure is ~1314 bar (19,057 psi).
- When to Use Bursting Pressure Charts: Use them for safety assessments or non-ASME designs to ensure a large margin between operating pressure and failure. In ASME B31.3, they’re for reference only, as allowable stress governs design.
- Design vs. Bursting Pressure: Design pressure (300 bar) is the safe operating limit based on allowable stress with safety factors. Bursting pressure (~1314 bar) is the theoretical failure point without safety factors.