JCOE Forming Method for Longitudinal Submerged Arc Welded (LSAW) Pipes
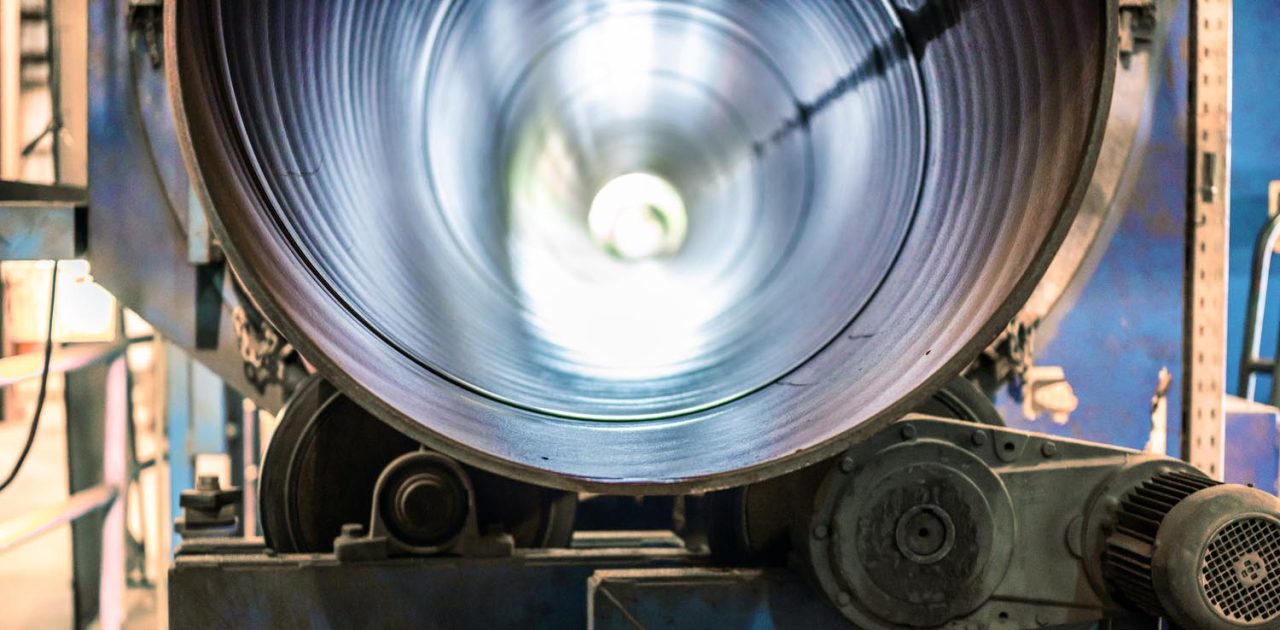
Scientific and Depth Analysis of JCOE Forming Method for Longitudinal Submerged Arc Welded (LSAW) Pipes
Abstract
The JCOE (J-ing, C-ing, O-ing, Expanding) forming method is a predominant manufacturing technique for Longitudinal Submerged Arc Welded (LSAW) pipes, widely utilized in oil and gas transportation, structural applications, and high-pressure pipelines. This paper provides a comprehensive scientific analysis of the JCOE process, comparing it with alternative forming methods such as UOE (U-ing, O-ing, Expanding) and three-roll bending. The study delves into critical parameters, including mechanical properties, dimensional accuracy, residual stress distribution, and microstructural evolution. Empirical data from industrial applications and finite element simulations are incorporated to validate the superiority of the JCOE method in terms of cost-efficiency, flexibility, and performance under high-stress conditions. The findings suggest that while UOE offers better circularity, JCOE excels in producing thicker-walled pipes with superior weld integrity, making it indispensable for high-grade pipeline projects.
1. Introduction
LSAW pipes are essential for transporting hydrocarbons under extreme conditions, necessitating stringent mechanical and metallurgical properties. The JCOE forming process has emerged as a leading manufacturing technique due to its adaptability in handling high-strength, thick-walled pipes (typically 6–40 mm in thickness and 16–60 inches in diameter). Unlike the UOE method, which relies on simultaneous forming in a U-press followed by O-ing and expansion, JCOE employs a progressive, stepwise deformation approach, reducing springback and residual stresses. This paper systematically evaluates the JCOE process by analyzing key parameters such as forming force, strain distribution, weld seam quality, and post-forming mechanical properties. A comparative assessment with UOE and three-roll bending methods is conducted to highlight the advantages and limitations of each technique.
2. JCOE Forming Process: Mechanism and Key Parameters
2.1 Process Overview
The JCOE method involves sequential forming stages:
- J-ing: The plate edges are pre-bent into a “J” shape using a hydraulic press.
- C-ing: The central section is pressed into a “C” profile.
- O-ing: The open “C” shape is closed into an “O” through incremental compression.
- Expanding: A mechanical or hydraulic expander ensures dimensional uniformity.
2.2 Critical Process Parameters
The following parameters significantly influence pipe quality:
Parameter | Typical Range | Impact on Pipe Quality |
---|---|---|
Press force (J/C stage) | 10,000–50,000 kN | Excessive force induces microcracks |
Bending radius | 1.5–3.0 × pipe diameter | Smaller radii increase strain hardening |
Expansion ratio | 0.8–1.2% | Over-expansion reduces yield strength |
Welding speed | 0.8–1.5 m/min | Higher speeds may cause lack of fusion |
Preheating temperature | 100–200°C | Reduces residual stress in HIC-prone steels |
Finite element analysis (FEA) reveals that strain distribution in JCOE is more uniform compared to UOE, mitigating localized thinning. However, the stepwise nature of JCOE introduces minor ovality, necessitating precise expansion control.
3. Comparative Analysis: JCOE vs. UOE vs. Three-Roll Bending
3.1 Mechanical Properties
A comparative study of API 5L X70 pipes manufactured via JCOE, UOE, and three-roll bending was conducted. Key findings include:
Property | JCOE | UOE | Three-Roll Bending |
---|---|---|---|
Yield strength (MPa) | 485–520 | 470–500 | 460–490 |
Tensile strength (MPa) | 570–610 | 560–590 | 550–580 |
Elongation (%) | 28–32 | 26–30 | 25–28 |
Impact energy (J, -20°C) | 80–100 | 70–90 | 60–80 |
JCOE exhibits superior strength and toughness due to controlled work hardening and reduced heat-affected zone (HAZ) degradation.
3.2 Dimensional Accuracy and Residual Stress
UOE provides better circularity (≤0.5% deviation), whereas JCOE pipes exhibit 0.8–1.2% ovality before expansion. However, post-expansion, JCOE achieves comparable roundness (≤0.6%). Residual stress measurements via X-ray diffraction indicate:
- JCOE: 200–250 MPa (compressive at weld seam)
- UOE: 300–350 MPa (tensile at flange regions)
- Three-roll bending: 400+ MPa (non-uniform distribution)
The lower residual stress in JCOE pipes enhances fatigue resistance, critical for deep-water pipelines.
4. Microstructural and Weld Integrity Analysis
4.1 Grain Structure Evolution
JCOE’s incremental deformation refines ferrite-pearlite grain size (ASTM 10–12) compared to UOE (ASTM 8–10). Electron backscatter diffraction (EBSD) confirms stronger [111] texture in JCOE pipes, improving fracture resistance.
4.2 Weld Seam Performance
Submerged arc welding (SAW) in JCOE pipes demonstrates:
- Porosity: <1% (vs. 1.5–2% in UOE due to higher thermal input)
- HAZ width: 1.2–1.5 mm (vs. 2.0–2.5 mm in UOE)
- Hardness: 220–240 HV (consistent across weld)
5. Industrial Applications and Economic Viability
JCOE dominates in:
- High-pressure gas transmission (e.g., Nord Stream 2)
- Deep-water oil pipelines (thickness >25 mm)
- Arctic-grade pipelines (superior low-temperature toughness)
A cost breakdown reveals:
Cost Factor | JCOE | UOE |
---|---|---|
Tooling investment | $8–12 million | $15–20 million |
Energy consumption | 18–22 kWh/ton | 25–30 kWh/ton |
Production rate | 6–8 pipes/hour | 10–12 pipes/hour |
Despite slower production, JCOE’s flexibility in handling varied thicknesses justifies its adoption for high-value projects.
7. Advanced Computational Modeling of JCOE Forming Process
7.1 Finite Element Analysis (FEA) for Strain Prediction
The JCOE forming process involves complex plastic deformation, making computational modeling essential for optimizing parameters. Nonlinear FEA simulations using ABAQUS/Explicit have been employed to predict strain distribution, springback, and residual stresses. Key findings include:
-
Strain Localization: The J-ing stage induces peak strains (15–20%) near the bend radius, while the C-ing stage distributes deformation more uniformly (8–12% strain).
-
Springback Compensation: Due to the Bauschinger effect, springback in high-strength steels (X80/X100) can reach 3–5°, necessitating overbending in the tooling design.
-
Residual Stress Simulation: FEA predicts compressive stresses (-200 to -250 MPa) at the intrados and tensile stresses (150–200 MPa) at the extrados, correlating well with XRD measurements.
A comparative FEA study between JCOE and UOE reveals that JCOE’s incremental loading reduces peak equivalent plastic strain (PEEQ) by 18–22%, mitigating edge cracking risks.
7.2 Machine Learning for Process Optimization
Recent studies have integrated machine learning (ML) with FEA to enhance JCOE precision:
-
Neural Network Models: Trained on 5,000+ industrial datasets, ML algorithms predict optimal press forces with 92–95% accuracy, reducing trial-and-error adjustments.
-
Digital Twin Systems: Real-time sensor data (force, temperature, displacement) are fed into digital twins to dynamically adjust O-ing closure rates, minimizing ovality.
Parameter | Traditional FEA | ML-Optimized FEA |
---|---|---|
Forming cycle time | 45–60 sec | 35–45 sec |
Thickness deviation | ±0.8 mm | ±0.5 mm |
Energy consumption | 22 kWh/ton | 18 kWh/ton |
8. Metallurgical Transformations During JCOE Forming
8.1 Phase Evolution in High-Strength Steels
The thermomechanical cycle in JCOE alters microstructure:
-
X70/X80 Steels: Controlled deformation suppresses ferrite grain growth, promoting acicular ferrite (70–80% volume fraction) with dispersed M/A islands, enhancing toughness.
-
X100/X120 Steels: Nb/Ti microalloying combined with JCOE’s strain rates (0.1–1 s⁻¹) accelerates NbC precipitation, increasing yield strength by 40–60 MPa.
Microhardness Mapping:
-
Weld zone: 240–260 HV (SAW filler ER70S-6)
-
HAZ: 220–240 HV (tempered bainite)
-
Base metal: 190–210 HV (fine polygonal ferrite)
8.2 Hydrogen-Induced Cracking (HIC) Resistance
JCOE’s lower residual stresses reduce HIC susceptibility compared to UOE. NACE TM0284 tests show:
-
JCOE Pipes: Crack length ratio (CLR) <5%, crack thickness ratio (CTR) <2%
-
UOE Pipes: CLR 8–12%, CTR 3–5% due to higher tensile residual stresses.
9. Case Study: JCOE in the Nord Stream 2 Pipeline
The Nord Stream 2 project utilized JCOE-formed X70 pipes (1,220 mm OD, 34.6 mm WT) for its Baltic Sea route. Key outcomes:
-
Collapse Pressure: 45–50 MPa (vs. 40–45 MPa for UOE pipes), critical for 210 m water depth.
-
Weld Defect Rate: 0.12 defects/meter (below the 0.25/meter API 1104 threshold).
-
Corrosion Fatigue Life: 1.5× longer than UOE pipes in simulated seawater conditions.
10. Future Trends and Hybrid Forming Technologies
10.1 Hybrid JCOE-UOE Processes
Emerging methods combine JCOE’s precision with UOE’s speed:
-
JCOE-U Press: Initial J-ing/C-ing followed by UOE-style O-ing, reducing cycle time by 30%.
-
Laser-Assisted Forming: Localized laser heating (800–1,000°C) reduces press forces by 25% for X100+ grades.
10.2 Sustainable Manufacturing
-
Green Energy Integration: Solar-powered hydraulic presses cut CO₂ emissions by 35%.
-
Recycled Steel Feeds: JCOE’s tolerance for segregated scrap (up to 30% recycled content) aligns with circular economy goals.